SMT verwendet herkömmliche Hohlraumanalysen und -lösungen für das Luft-Reflow-Schweißen von Lotpasten (2023 Essence Edition), Sie haben es verdient!
1 Einleitung

Bei der Leiterplattenbestückung wird zunächst Lotpaste auf das Lötpad der Leiterplatte gedruckt und anschließend werden verschiedene elektronische Bauteile befestigt. Schließlich werden nach dem Reflow-Ofen die Zinnperlen in der Lötpaste geschmolzen und alle Arten von elektronischen Bauteilen und das Lötpad der Leiterplatte zusammengeschweißt, um den Zusammenbau elektrischer Submodule zu realisieren. Surfacemount-Technologie (SMT) wird zunehmend in hochdichten Verpackungsprodukten eingesetzt, wie z. B. System Level Package (SIP), Ballgridarray (BGA)-Geräten und Power Bare Chip, Square Flat Pin-less Package (Quad Aat No-Lead, bezeichnet als QFN). ) Gerät.
Aufgrund der Eigenschaften des Lötpastenschweißprozesses und der Materialien entstehen nach dem Reflow-Schweißen dieser Geräte mit großer Lötoberfläche Löcher im Lötschweißbereich, die sich auf die elektrischen Eigenschaften, thermischen Eigenschaften und mechanischen Eigenschaften des Produkts auswirken Dies kann sogar zu Produktfehlern führen. Daher ist die Verbesserung des Lötpasten-Reflow-Schweißhohlraums zu einem Prozess- und technischen Problem geworden, das gelöst werden muss. Einige Forscher haben die Ursachen des BGA-Lötkugelschweißhohlraums analysiert und untersucht und Verbesserungslösungen für herkömmliches Lot bereitgestellt Pasten-Reflow-Schweißverfahren Schweißbereich von Bei QFN von mehr als 10 mm2 oder einer Schweißfläche von mehr als 6 mm2 fehlt die Bare-Chip-Lösung.
Verwenden Sie Preformlot-Schweißen und Vakuum-Rückflussofenschweißen, um das Schweißloch zu verbessern. Vorgefertigtes Lot erfordert spezielle Ausrüstung, um das Flussmittel zu punktieren. Beispielsweise wird der Chip stark versetzt und geneigt, nachdem er direkt auf dem vorgefertigten Lot platziert wurde. Wenn der Flussmittel-Montagechip aufgeschmolzen und dann gespitzt wird, verlängert sich der Prozess um zwei Aufschmelzvorgänge, und die Kosten für vorgefertigtes Lot- und Flussmittelmaterial sind viel höher als für die Lotpaste.
Vakuum-Reflux-Geräte sind teurer, die Vakuumkapazität der unabhängigen Vakuumkammer ist sehr gering, die Kostenleistung ist nicht hoch und das Problem der Zinnspritzer ist schwerwiegend, was ein wichtiger Faktor bei der Anwendung von hoher Dichte und kleinem Abstand ist Produkte. In diesem Artikel wird auf der Grundlage des herkömmlichen Lötpasten-Reflow-Schweißverfahrens ein neues sekundäres Reflow-Schweißverfahren entwickelt und eingeführt, um den Schweißhohlraum zu verbessern und die Probleme der Verbindung und der durch den Schweißhohlraum verursachten Kunststoffdichtungsrisse zu lösen.
2 Lötpastendruck-Reflow-Schweißhohlraum und Produktionsmechanismus
2.1 Schweißhohlraum
Nach dem Reflow-Schweißen wurde das Produkt einer Röntgenprüfung unterzogen. Es wurde festgestellt, dass die Löcher in der Schweißzone mit hellerer Farbe auf unzureichendes Lot in der Schweißschicht zurückzuführen waren, wie in Abbildung 1 dargestellt
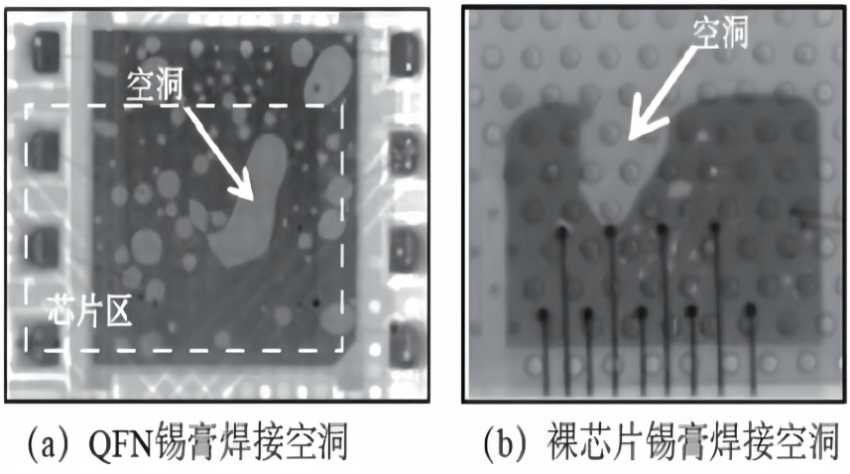
Röntgendetektion des Blasenlochs
2.2 Entstehungsmechanismus des Schweißhohlraums
Am Beispiel der Lotpaste sAC305 sind die Hauptzusammensetzung und Funktion in Tabelle 1 aufgeführt. Das Flussmittel und die Zinnperlen werden in Pastenform miteinander verbunden. Das Gewichtsverhältnis von Zinnlot zu Flussmittel beträgt etwa 9:1 und das Volumenverhältnis etwa 1:1.
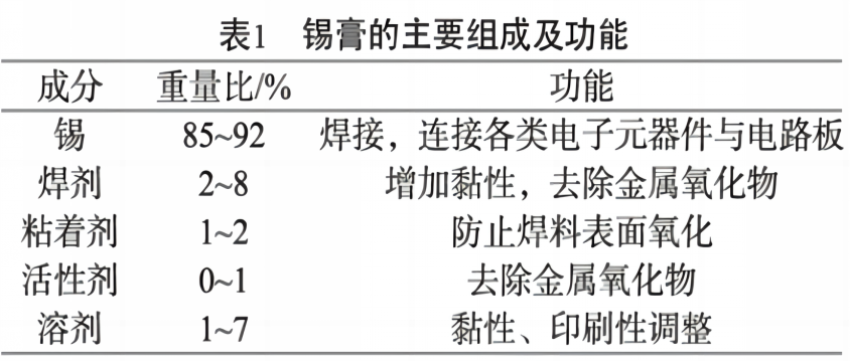
Nachdem die Lotpaste gedruckt und mit verschiedenen elektronischen Komponenten bestückt wurde, durchläuft die Lotpaste beim Durchgang durch den Rückflussofen vier Stufen des Vorheizens, der Aktivierung, des Rückflusses und des Abkühlens. Auch der Zustand der Lotpaste ist bei unterschiedlichen Temperaturen in verschiedenen Stadien unterschiedlich, wie in Abbildung 2 dargestellt.
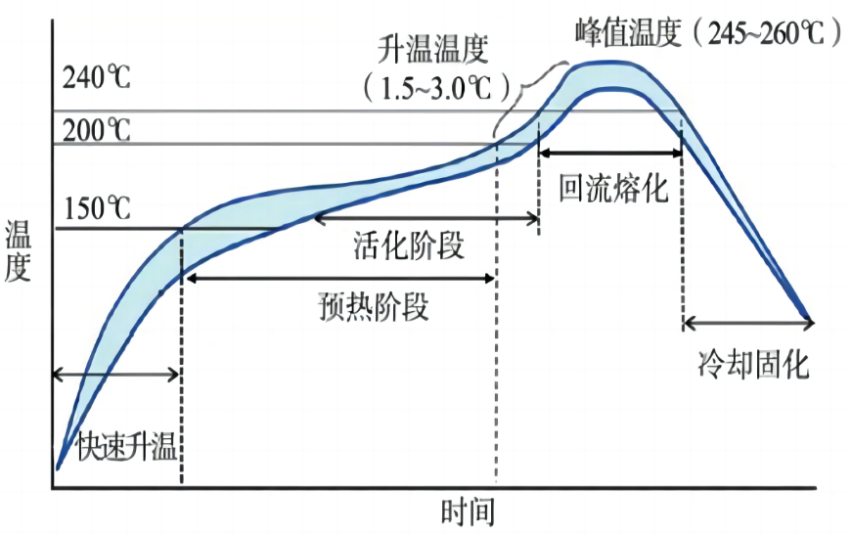
Profilreferenz für jeden Bereich des Reflow-Lötens
In der Vorheiz- und Aktivierungsphase verflüchtigen sich die flüchtigen Bestandteile des Flussmittels in der Lotpaste beim Erhitzen in Gas. Gleichzeitig entstehen Gase, wenn das Oxid auf der Oberfläche der Schweißschicht entfernt wird. Einige dieser Gase verflüchtigen sich und verlassen die Lotpaste, und die Lotperlen werden aufgrund der Verflüchtigung des Flussmittels fest kondensiert. In der Rückflussphase verdunstet das verbleibende Flussmittel in der Lötpaste schnell, die Zinnkügelchen schmelzen, eine kleine Menge flüchtiges Flussmittelgas und der größte Teil der Luft zwischen den Zinnkügelchen werden nicht rechtzeitig verteilt, und der Rest in der Geschmolzenes Zinn und unter der Spannung des geschmolzenen Zinns bilden eine Hamburger-Sandwichstruktur und werden vom Lötpad der Leiterplatte und den elektronischen Bauteilen aufgefangen, und das im flüssigen Zinn eingeschlossene Gas kann nur durch den Auftrieb nach oben nur schwer entweichen. Die obere Schmelzzeit beträgt sehr kurz. Wenn das geschmolzene Zinn abkühlt und zu festem Zinn wird, entstehen Poren in der Schweißschicht und es bilden sich Lötlöcher, wie in Abbildung 3 dargestellt.
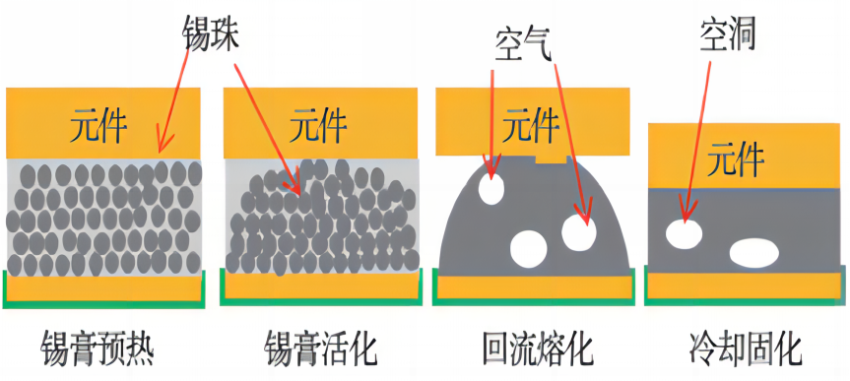
Schematische Darstellung eines Hohlraums, der durch das Lötpasten-Reflow-Schweißen entsteht
Die Hauptursache für Schweißhohlräume liegt darin, dass die Luft oder das flüchtige Gas, das nach dem Schmelzen in der Lötpaste eingeschlossen ist, nicht vollständig entladen wird. Zu den Einflussfaktoren gehören das Lotpastenmaterial, die Form des Lotpastendrucks, die Menge des Lotpastendrucks, die Rückflusstemperatur, die Rückflusszeit, die Schweißgröße, die Struktur usw.
3. Überprüfung der Einflussfaktoren beim Drucken von Reflow-Schweißlöchern mit Lötpaste
QFN- und Bare-Chip-Tests wurden verwendet, um die Hauptursachen für Hohlräume beim Reflow-Schweißen zu bestätigen und Möglichkeiten zur Verbesserung der durch Lotpaste gedruckten Hohlräume beim Reflow-Schweißen zu finden. Das Profil des QFN- und Bare-Chip-Lötpasten-Reflow-Schweißprodukts ist in Abbildung 4 dargestellt. Die Größe der QFN-Schweißfläche beträgt 4,4 mm x 4,1 mm, die Schweißfläche besteht aus einer verzinnten Schicht (100 % reines Zinn); Die Schweißgröße des blanken Chips beträgt 3,0 mm x 2,3 mm, die Schweißschicht ist eine gesputterte Nickel-Vanadium-Bimetallschicht und die Oberflächenschicht besteht aus Vanadium. Das Schweißpad des Substrats bestand aus stromlosem Nickel-Palladium-Gold-Tauchen und die Dicke betrug 0,4 μm/0,06 μm/0,04 μm. Es wird SAC305-Lötpaste verwendet, die Lötpastendruckausrüstung ist DEK Horizon APix, die Rückflussofenausrüstung ist BTUPyramax150N und die Röntgenausrüstung ist DAGExD7500VR.
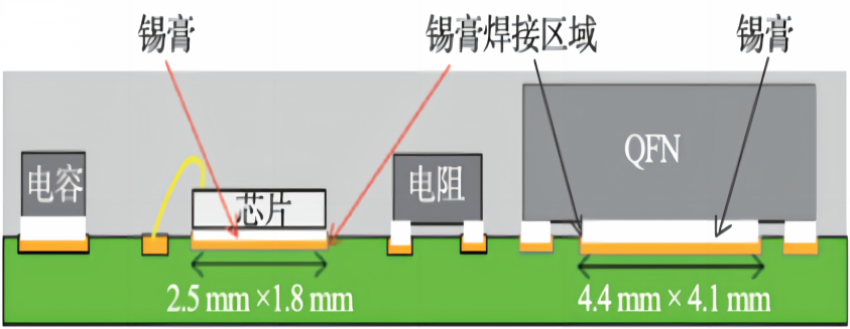
QFN- und Bare-Chip-Schweißzeichnungen
Um den Vergleich der Testergebnisse zu erleichtern, wurde das Reflow-Schweißen unter den Bedingungen in Tabelle 2 durchgeführt.
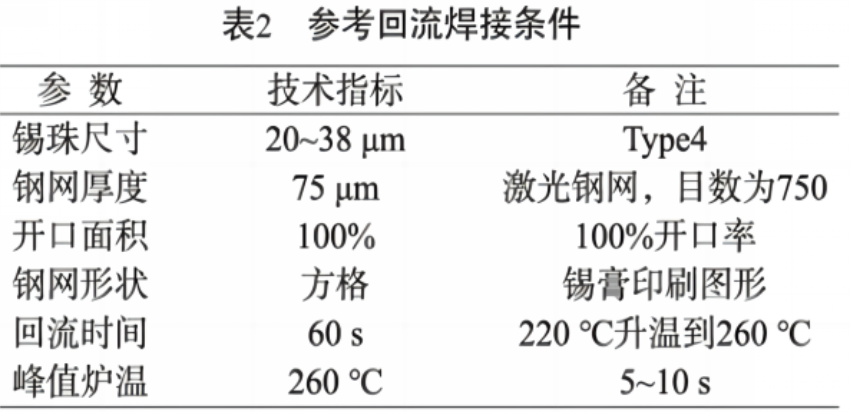
Tabelle der Reflow-Schweißbedingungen
Nachdem die Oberflächenmontage und das Reflow-Schweißen abgeschlossen waren, wurde die Schweißschicht durch Röntgenstrahlen erkannt und es wurde festgestellt, dass sich große Löcher in der Schweißschicht an der Unterseite des QFN und des blanken Chips befanden, wie in Abbildung 5 dargestellt.
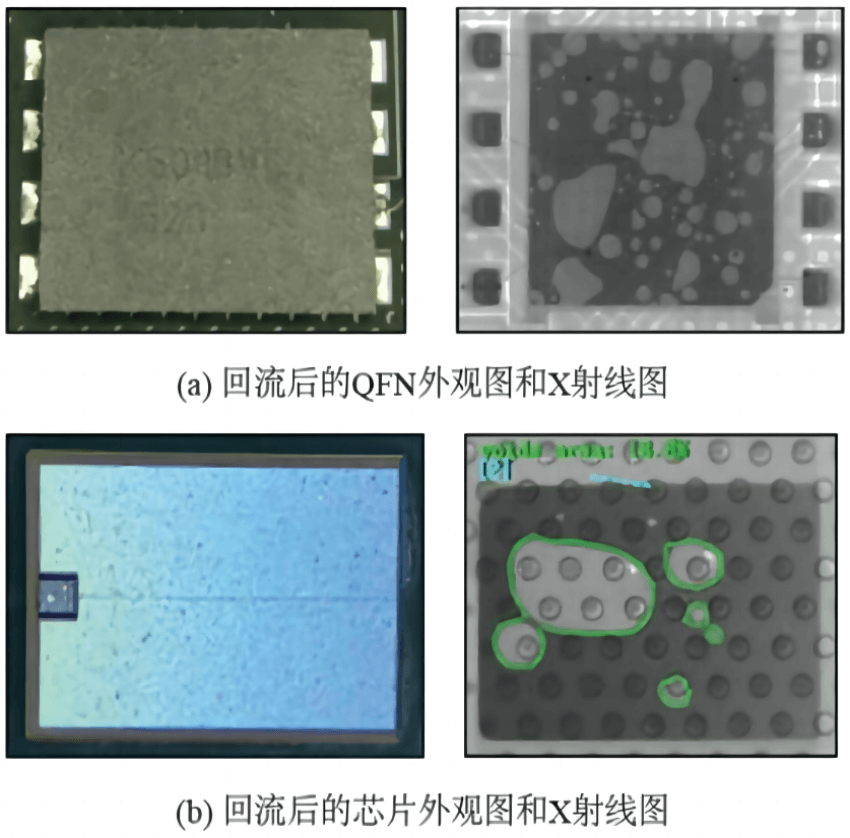
QFN und Chip-Hologramm (Röntgen)
Da sich die Größe der Zinnperlen, die Dicke des Stahlgeflechts, die Öffnungsfläche, die Form des Stahlgeflechts, die Rückflusszeit und die maximale Ofentemperatur auf die Hohlräume beim Reflow-Schweißen auswirken, gibt es viele Einflussfaktoren, die direkt durch DOE-Tests und die Anzahl der Versuche überprüft werden Gruppen werden zu groß sein. Es ist notwendig, die Haupteinflussfaktoren schnell durch Korrelationsvergleichstests zu überprüfen und zu bestimmen und diese dann durch DOE weiter zu optimieren.
3.1 Abmessungen von Lötlöchern und Lötpasten-Zinnperlen
Beim Lotpastentest Typ 3 (Perlengröße 25–45 μm) SAC305 bleiben die übrigen Bedingungen unverändert. Nach dem Reflow werden die Löcher in der Lotschicht gemessen und mit Lotpaste Typ 4 verglichen. Es wurde festgestellt, dass sich die Löcher in der Lotschicht zwischen den beiden Arten von Lotpaste nicht wesentlich unterscheiden, was darauf hindeutet, dass die Lotpaste mit unterschiedlicher Perlengröße keinen offensichtlichen Einfluss auf die Löcher in der Lotschicht hat, was keinen Einflussfaktor darstellt. wie in FIG. 6 Wie abgebildet.
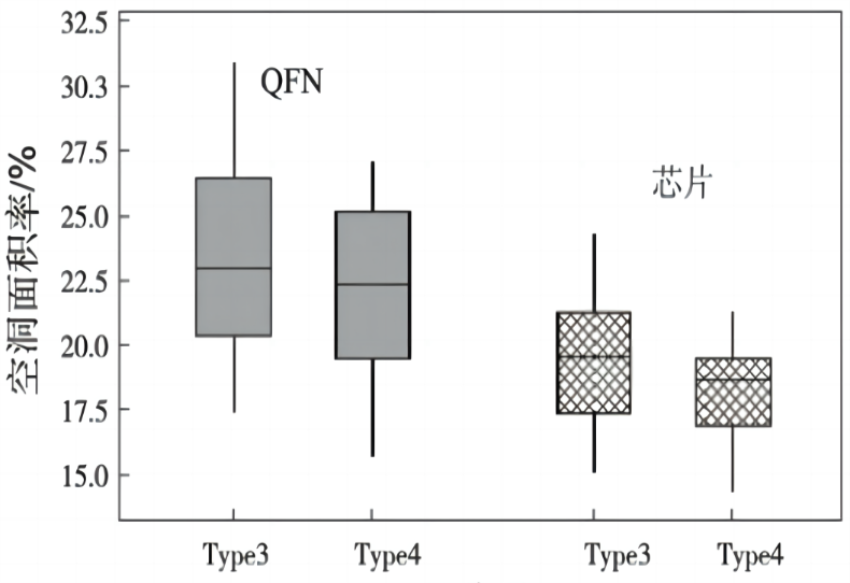
Vergleich von metallischen Zinnpulverlöchern mit unterschiedlichen Partikelgrößen
3.2 Dicke des Schweißhohlraums und des bedruckten Stahlgewebes
Nach dem Aufschmelzen wurde die Hohlraumfläche der geschweißten Schicht mit dem gedruckten Stahlgewebe mit einer Dicke von 50 μm, 100 μm und 125 μm gemessen, und die anderen Bedingungen blieben unverändert. Es wurde festgestellt, dass die Wirkung unterschiedlicher Dicke des Stahlgeflechts (Lötpaste) auf QFN mit der des gedruckten Stahlgeflechts mit einer Dicke von 75 μm verglichen wurde. Mit zunehmender Dicke des Stahlgeflechts nimmt die Hohlraumfläche allmählich und langsam ab. Nach Erreichen einer bestimmten Dicke (100 μm) kehrt sich die Hohlraumfläche um und beginnt mit zunehmender Dicke des Stahlgeflechts zuzunehmen, wie in Abbildung 7 dargestellt.
Dies zeigt, dass bei einer Erhöhung der Lotpastenmenge das flüssige Zinn mit Rückfluss vom Chip bedeckt wird und der Auslass der Restluft nur an vier Seiten schmal ist. Wenn die Menge der Lotpaste geändert wird, erhöht sich auch der Auslass der Restluft, und der sofortige Luftstoß, der in flüssiges Zinn oder flüchtiges Gas gewickelt ist und aus flüssigem Zinn entweicht, führt dazu, dass flüssiges Zinn um QFN und den Chip spritzt.
Der Test ergab, dass mit zunehmender Dicke des Stahlgeflechts auch das Platzen von Blasen durch das Entweichen von Luft oder flüchtigem Gas zunimmt und die Wahrscheinlichkeit, dass Zinn um QFN und Chip herumspritzt, entsprechend zunimmt.
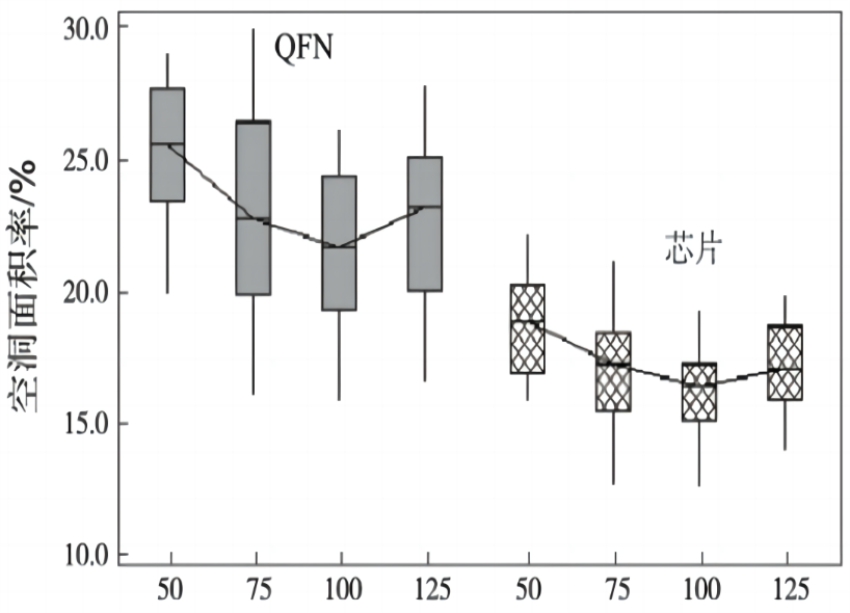
Vergleich von Löchern in Stahlgeflechten unterschiedlicher Dicke
3.3 Flächenverhältnis von Schweißhohlraum und Stahlgitteröffnung
Das bedruckte Stahlgewebe wurde mit einer Öffnungsrate von 100 %, 90 % und 80 % getestet, die übrigen Bedingungen blieben unverändert. Nach dem Aufschmelzen wurde die Hohlraumfläche der geschweißten Schicht gemessen und mit dem gedruckten Stahlgewebe mit einer Öffnungsrate von 100 % verglichen. Es wurde festgestellt, dass es unter den Bedingungen einer Öffnungsrate von 100 % und 90 % 80 % keinen signifikanten Unterschied im Hohlraum der geschweißten Schicht gab, wie in Abbildung 8 dargestellt.
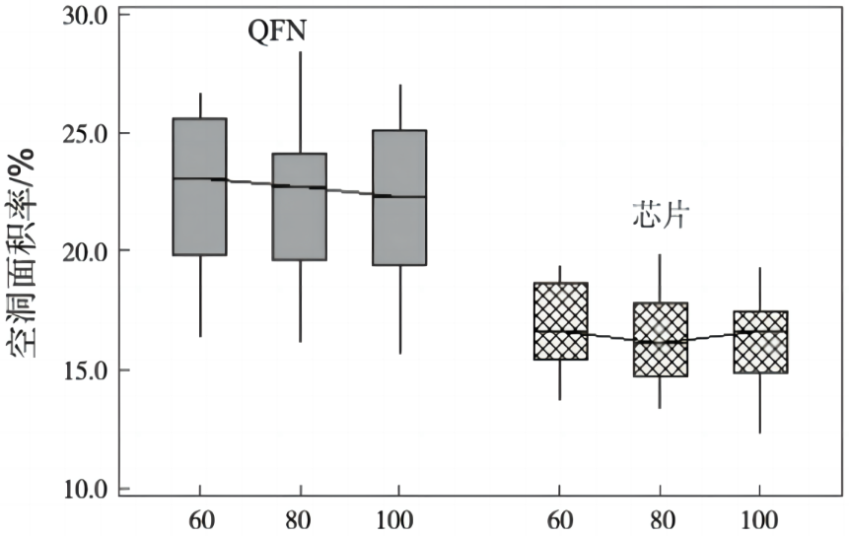
Hohlraumvergleich unterschiedlicher Öffnungsflächen unterschiedlicher Stahlgeflechte
3.4 Geschweißter Hohlraum und bedruckte Stahlgitterform
Beim Druckformtest der Lotpaste von Streifen b und Schräggitter c bleiben die übrigen Bedingungen unverändert. Nach dem Aufschmelzen wird die Hohlraumfläche der Schweißschicht gemessen und mit der Druckform des Gitters a verglichen. Es wurde festgestellt, dass es unter den Bedingungen von Gitter, Streifen und geneigtem Gitter keinen signifikanten Unterschied im Hohlraum der Schweißschicht gibt, wie in Abbildung 9 dargestellt.
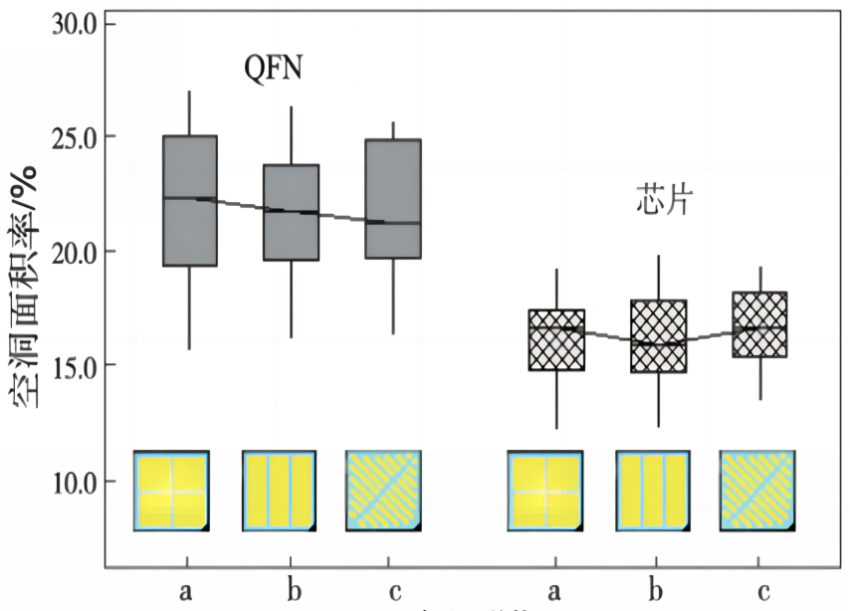
Vergleich von Löchern in verschiedenen Öffnungsarten von Stahlgeflechten
3.5 Schweißhohlraum und Rückflusszeit
Nach einem Test mit verlängerter Rückflusszeit (70 s, 80 s, 90 s) blieben die anderen Bedingungen unverändert. Das Loch in der Schweißschicht wurde nach dem Rückfluss gemessen und mit der Rückflusszeit von 60 s verglichen. Es wurde festgestellt, dass mit der Zunahme von Während der Rückflusszeit nahm die Schweißlochfläche ab, aber die Reduktionsamplitude nahm mit zunehmender Zeit allmählich ab, wie in Abbildung 10 dargestellt. Dies zeigt, dass im Falle einer unzureichenden Rückflusszeit eine Verlängerung der Rückflusszeit förderlich ist bis zum vollständigen Überlauf der in geschmolzenes flüssiges Zinn gehüllten Luft, aber nachdem die Rückflusszeit auf eine bestimmte Zeit ansteigt, ist es für die in flüssiges Zinn gehüllte Luft schwierig, wieder überzulaufen. Die Rückflusszeit ist einer der Faktoren, die den Schweißhohlraum beeinflussen.
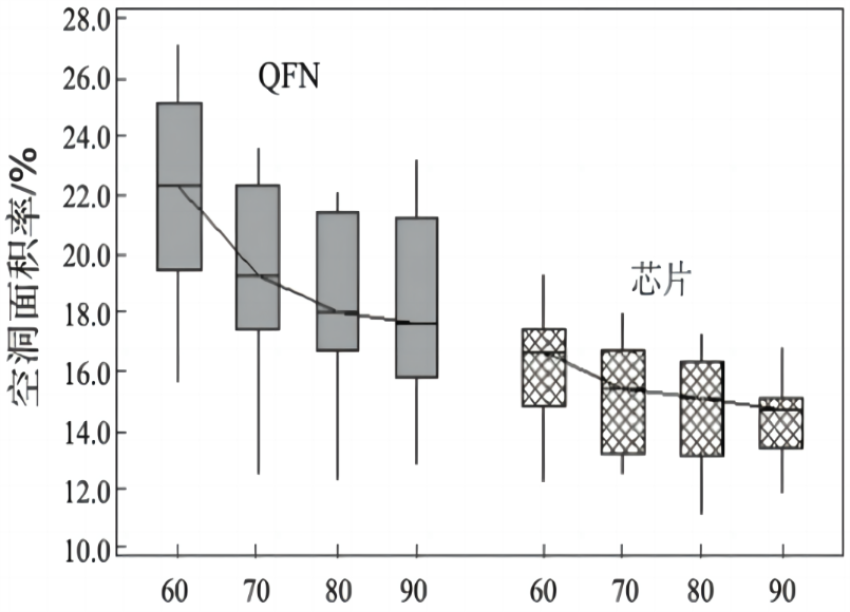
Vergleich unterschiedlicher Refluxzeiten entfällt
3.6 Schweißraum und Spitzenofentemperatur
Bei 240 ℃ und 250 ℃ Spitzenofentemperaturtests und anderen unveränderten Bedingungen wurde die Hohlraumfläche der geschweißten Schicht nach dem Reflow gemessen und mit 260 ℃ Spitzenofentemperatur verglichen, wurde festgestellt, dass unter verschiedenen Spitzenofentemperaturbedingungen der Hohlraum von Die verschweißte Schicht aus QFN und Chip hat sich nicht wesentlich verändert, wie in Abbildung 11 dargestellt. Es zeigt, dass unterschiedliche Spitzenofentemperaturen keinen offensichtlichen Einfluss auf QFN und das Loch in der Schweißschicht des Chips haben. was kein Einflussfaktor ist.
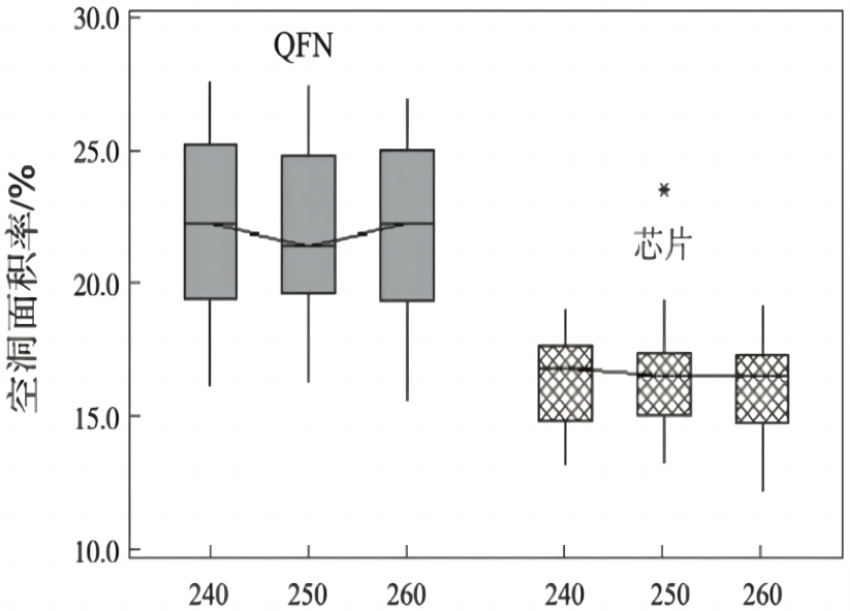
Vergleich verschiedener Spitzentemperaturen entfällt
Die oben genannten Tests zeigen, dass die wesentlichen Faktoren, die den Hohlraum der Schweißschicht von QFN und Chip beeinflussen, die Rückflusszeit und die Dicke des Stahlgeflechts sind.
4 Verbesserung des Reflow-Schweißhohlraums beim Lötpastendruck
4.1DOE-Test zur Verbesserung des Schweißhohlraums
Das Loch in der Schweißschicht aus QFN und Chip wurde verbessert, indem der optimale Wert der Haupteinflussfaktoren (Rückflusszeit und Stahlnetzdicke) ermittelt wurde. Bei der Lötpaste handelte es sich um SAC305 Typ 4, das Stahlgeflecht war gitterförmig (100 % Öffnungsgrad), die maximale Ofentemperatur betrug 260 °C und die übrigen Testbedingungen entsprachen denen der Testausrüstung. Der DOE-Test und die Ergebnisse sind in Tabelle 3 dargestellt. Die Einflüsse der Stahlgeflechtdicke und der Rückflusszeit auf QFN- und Spanschweißlöcher sind in Abbildung 12 dargestellt. Durch die Wechselwirkungsanalyse der Haupteinflussfaktoren wurde festgestellt, dass eine Stahlgeflechtdicke von 100 μm verwendet wird und 80 s Rückflusszeit können den Schweißhohlraum von QFN und Chip deutlich reduzieren. Die Schweißhohlraumrate von QFN wird von maximal 27,8 % auf 16,1 % reduziert, und die Schweißhohlraumrate von Spänen wird von maximal 20,5 % auf 14,5 % reduziert.
Im Test wurden 1000 Produkte unter optimalen Bedingungen (100 μm Stahlgewebedicke, 80 s Rückflusszeit) hergestellt und die Schweißhohlraumrate von 100 QFN und Span stichprobenartig gemessen. Die durchschnittliche Schweißhohlraumrate von QFN betrug 16,4 % und die durchschnittliche Schweißhohlraumrate des Chips betrug 14,7 %. Die Schweißhohlraumrate des Chips und des Chips ist offensichtlich reduziert.
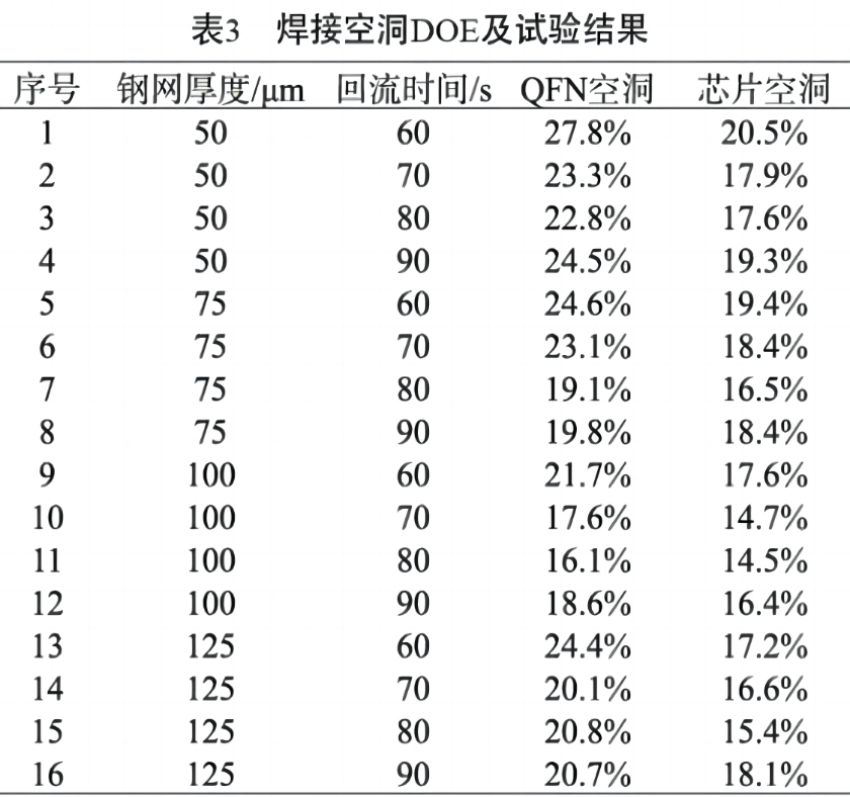
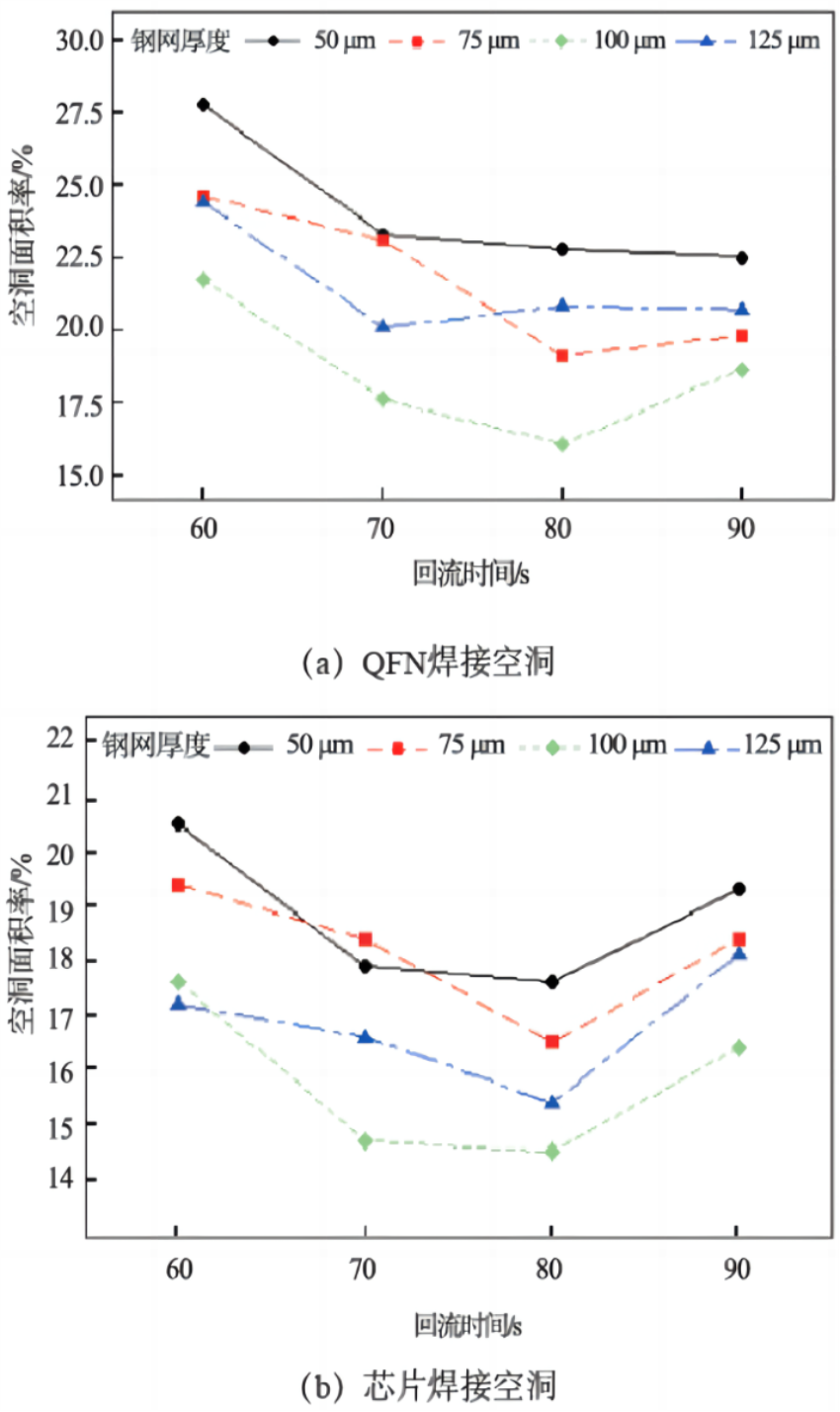
4.2 Das neue Verfahren verbessert den Schweißhohlraum
Die tatsächliche Produktionssituation und der Test zeigen, dass bei einer Schweißkavitätsfläche an der Unterseite des Chips weniger als 10 % das Problem der Rissbildung in der Chipkavitätsposition während des Bleibondens und Formens nicht auftritt. Die durch DOE optimierten Prozessparameter können die Anforderungen zur Analyse und Lösung der Löcher beim herkömmlichen Lotpasten-Reflow-Schweißen nicht erfüllen, und die Schweißhohlraumfläche des Chips muss weiter reduziert werden.
Da der Chip, der mit dem Lot bedeckt ist, das Entweichen des Gases im Lot verhindert, wird die Lochrate an der Unterseite des Chips weiter reduziert, indem das mit Lot bedeckte Gas eliminiert oder reduziert wird. Es wird ein neuer Prozess des Reflow-Schweißens mit zwei Lotpastendrucken eingeführt: ein Lotpastendruck, ein Reflow, der QFN nicht abdeckt, und ein Bare-Chip, der das Gas im Lot abgibt; Der spezifische Prozess des sekundären Lotpastendrucks, des Patches und des sekundären Rückflusses ist in Abbildung 13 dargestellt.
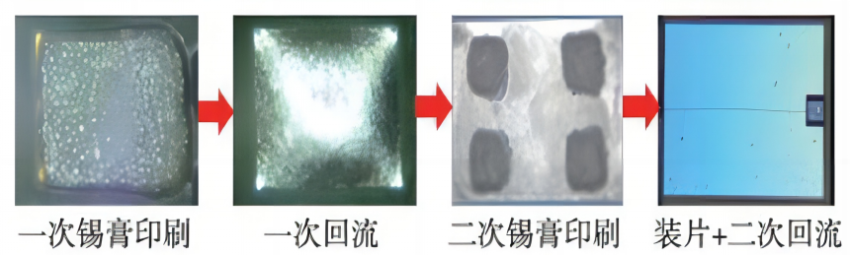
Wenn die 75 μm dicke Lotpaste zum ersten Mal gedruckt wird, entweicht der größte Teil des Gases im Lot ohne Chipabdeckung von der Oberfläche, und die Dicke nach dem Rückfluss beträgt etwa 50 μm. Nach Abschluss des primären Rückflusses werden kleine Quadrate auf die Oberfläche des abgekühlten, erstarrten Lots gedruckt (um die Menge an Lotpaste zu reduzieren, die Menge des Gasüberlaufs zu reduzieren, Lotspritzer zu reduzieren oder zu beseitigen) und die Lotpaste mit Eine Dicke von 50 μm (die obigen Testergebnisse zeigen, dass 100 μm am besten ist, sodass die Dicke des Sekundärdrucks 100 μm beträgt. 50 μm = 50 μm), dann den Chip installieren und dann durchfahren 80er Jahre. Nach dem ersten Drucken und Aufschmelzen gibt es fast keine Löcher im Lot, und die Lotpaste beim zweiten Drucken ist klein und das Schweißloch ist klein, wie in Abbildung 14 dargestellt.
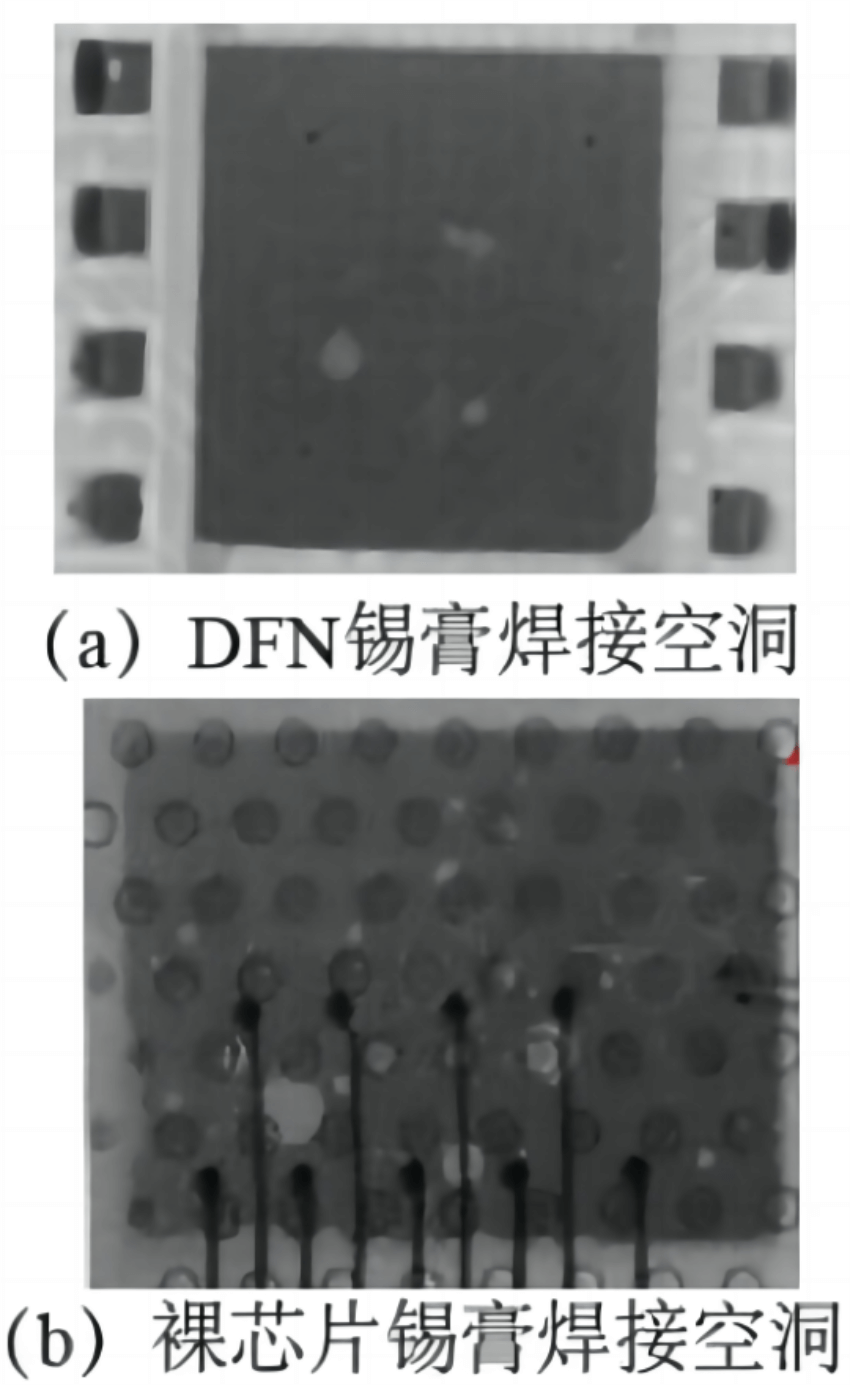
Nach zwei Drucken von Lotpaste, Hohlzeichnung
4.3 Überprüfung des Schweißhohlraumeffekts
Produktion von 2000 Produkten (die Dicke des ersten Druckstahlgewebes beträgt 75 μm, die Dicke des zweiten Druckstahlgewebes beträgt 50 μm), andere Bedingungen unverändert, zufällige Messung von 500 QFN und Spanschweißhohlraumrate, festgestellt, dass der neue Prozess nach dem ersten Rückfluss kein Hohlraum, nach dem zweiten Rückfluss QFN Der maximale Schweißhohlraumanteil beträgt 4,8 % und der maximale Schweißhohlraumanteil des Chips beträgt 4,1 %. Im Vergleich zum ursprünglichen Einpasten-Druckschweißverfahren und dem DOE-optimierten Verfahren wird der Schweißhohlraum erheblich reduziert, wie in Abbildung 15 dargestellt. Nach Funktionstests aller Produkte wurden keine Spanrisse festgestellt.
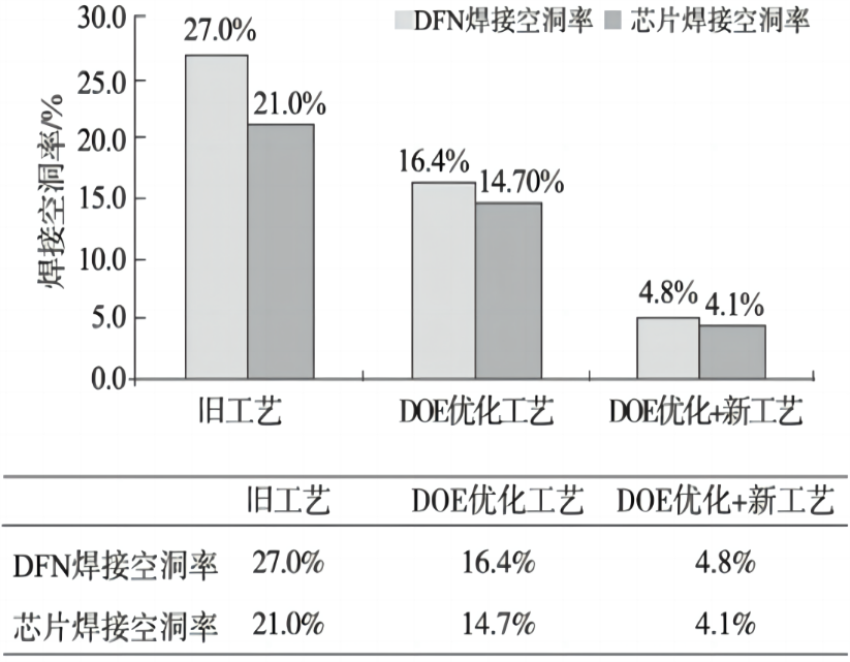
5 Zusammenfassung
Durch die Optimierung der Druckmenge der Lotpaste und der Rückflusszeit kann die Fläche des Schweißhohlraums reduziert werden, die Schweißhohlraumrate ist jedoch immer noch groß. Durch die Verwendung von zwei Reflow-Schweißtechniken mit Lotpastendruck kann die Schweißhohlraumrate effektiv und maximiert werden. Die Schweißfläche des blanken QFN-Schaltkreischips kann in der Massenproduktion 4,4 mm x 4,1 mm bzw. 3,0 mm x 2,3 mm betragen. Die Hohlraumrate beim Reflow-Schweißen wird auf unter 5 % kontrolliert, was die Qualität und Zuverlässigkeit des Reflow-Schweißens verbessert. Die Forschung in diesem Artikel liefert eine wichtige Referenz zur Verbesserung des Schweißhohlraumproblems bei großflächigen Schweißflächen.